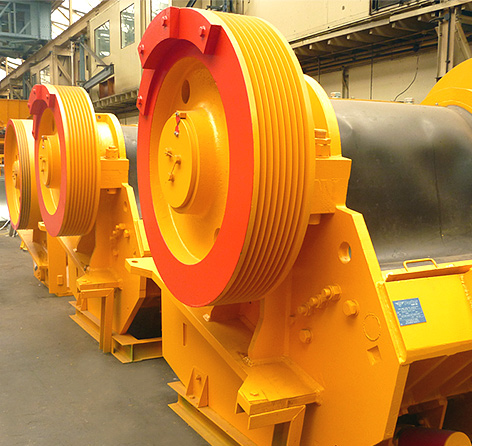
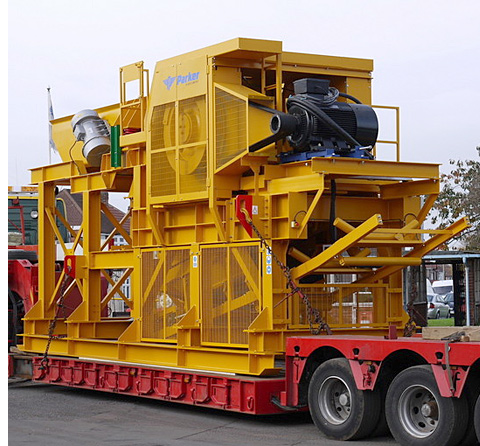
Jaw Crushers
First stage, primary rock crushing plants
Parker have been engineering rock crushers for over 100 years and today thousands of jaw crushing machines and units have been installed around the world.
Jaw crushers are used mainly in first stage, primary crushing applications and are ideal for use in quarries and recycling demolition operations. The two main types of jaw crusher produced by Parker are both single toggle designs with the up-thrust toggle RockSizer / StoneSizer model and down-thrust toggle RockSledger model.
Base Units
The RockSizer / StoneSizer up-thrust single toggle design has specific features that benefit the user with lower manganese wear rates and power consumption per tonne of material crushed with improved product shape whilst maintaining higher outputs than old double-toggle style designs. The ten standard models in the RockSizer / StoneSizer range cover output capacities from 5tph to over 200tph.
The RockSledger down-thrust single toggle design provides a more aggressive crushing motion and subsequently higher capacities are achieved. Six standard models in the RockSledger range provide outputs from 70tph to over 850tph and are at the core of the designs used by Parker in their ranges of static, transportable and mobile jaw crushing plants.
Features of both model ranges include:
- All steel fabricated body with single steel plate walls and side stiffening webs
- High quality nickel chrome, fully machined eccentric shaft
- Self-aligning spherical roller bearings are grease lubricated with valves to prevent over greasing
- Machined cast steel jaw stock with deep integral stiffening webs for lightness and high strength
- High quality iron casting toggle plates radially machined to reduce rubbing and wear
- Wedge locked, manganese steel corrugated tooth jaw plates are reversible to extend wear life
- Wear resistant liner plates fitted to sides of crushing chamber for protection of inlet and outlet
- Hydraulically assisted jaw adjustment and groove block shim placement
- Balanced flywheels are designed to ensure kinetic inertia is maintained for higher throughputs
- Options for mounting within static and mobile plant configurations
Rocksledger Jaw Crushers
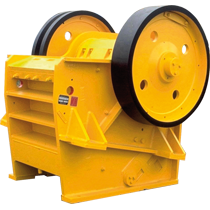
For primary stage medium to high capacity hard rock crushing or demolition applications
RockSledger jaw crushers feature massive, stress relieved, single plate walls with deep and substantial external side stiffeners and a high quality forged steel eccentric shaft.
The shaft is fully machined and has a ground finish on all bearing contact surfaces to increase resistance to shock loadings resulting in longer machine life.
Size of Crusher | Maximum Cube Feed Size (mm) | Approximate Weight (Kg) | No. & size of Vee Belt | Power to Drive (kW) | Jaw Setting: (mm) | |||||||||
50 | 65 | 75 | 100 | 125 | 150 | 175 | 200 | 250 | 300 | |||||
900 x 600 | 560 | 15,000 | 6 SPC | 90 | 70-90 | 75-105 | 90-130 | 110-170 | 130-210 | 150-250 | 170-290 | 190-330 | ||
1100 x 630 | 605 | 18,000 | 8 SPC | 110 | 80-110 | 100-125 | 135-175 | 175-220 | 210-265 | 250-310 | 290-350 | |||
1100 x 650 | 625 | 18,000 | 8 SPC | 110 | 100-125 | 135-175 | 175-220 | 210-265 | 250-310 | 290-350 | ||||
1100 x 760 | 710 | 26,945 | 8 SPC | 110 | 100-125 | 140-175 | 175-220 | 210-265 | 250-310 | 290-350 | ||||
1100 x 800 | 760 | 26,945 | 8 SPC | 110 | 140-175 | 175-220 | 210-265 | 250-310 | 290-350 | |||||
1300 x 1050 | 1000 | 38,000 | 12 SPC | 200 | 310-380 | 365-450 | 475-570 | 590-715 | 730-870 |
Rocksizer Jaw Crushers
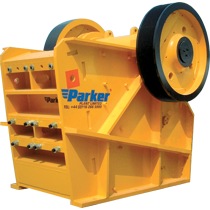
RockSizer primary stage jaw crushers feature the upthrust toggle action which is also common to the StoneSizer range. Developed by Parker, this gives a slight downward movement to the swing jaw that promotes a forced feed and therefore increased output while at the same time minimising any rubbing action resulting in a well shaped product and reduced and even wear on the crushing jaws.
Size of Crusher | Max Cube Feed Size | Approximate Weight | No. & size of Vee Belt | Power to Drive | Jaw Setting: (mm) | |||||||
(mm) | (kg) | (kW) | 30 | 40 | 50 | 65 | 75 | 100 | 125 | 150 | ||
600 x 300 | 280 | 4,200 | 4 SPC | 30 | 25-35 | 30-45 | 35-55 | 40-65 | 45-75 | |||
700 x 450 | 410 | 6,700 | 5 SPC | 37 | 35-45 | 46-60 | 50-65 | 65-85 | 80-105 | 100-130 | ||
800 x 480 | 435 | 10,260 | 4 SPC | 55 | 38-49 | 50-65 | 60-80 | 75-100 | 90-120 | 105-140 | ||
800 x 500 | 455 | 10,260 | 4 SPC | 55 | 50-65 | 60-80 | 75-100 | 90-120 | 105-140 | |||
950 x 300 | 280 | 6,685 | 4 SPC | 45 | 40-55 | 50-65 | 60-80 | 70-90 | 80-105 | |||
1000 x 600 | 575 | 16,600 | 8 SPC | 110 | 85-105 | 100-135 | 125-160 | 140-190 | 165-210 | |||
1000 x 625 | 600 | 16,600 | 8 SPC | 110 | 100-135 | 125-160 | 140-190 | 165-210 | ||||
1200 x 300 | 280 | 11,175 | 5 SPC | 90 | 55-75 | 65-90 | 80-105 | 95-125 | 105-135 |
Static Jaw Crushers
RockRanger RF & RD
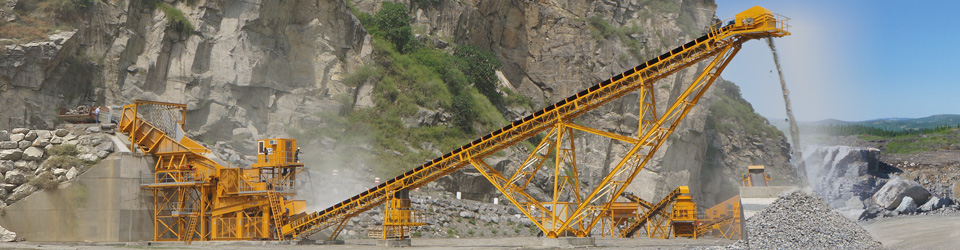
The purpose-built RockRanger is suitable for both quarry and demolition applications and incorporates a vibrating feeder with replaceable grizzly section and the option of a Vibrating Grizzly Screen.
The RockRanger has a wide discharge conveyor with good clearance under the crusher. Installation is rapid and easy to set up. The feed hopper is an externally reinforced heavy-duty steel plate hopper to stand up to the toughest of jobs.
- RockSledger / RockSizer heavy-duty jaw crusher
- Heavy duty feeder with grizzly section
- Hydraulically assisted adjustment setting
- Roller bearing protected by grease filled labyrinths
- Improved high performance manganese jaws
- Adaptors for bearing condition monitoring
- Low profile European design
- Suitable for quarrying, demolition & recycling applications
Features
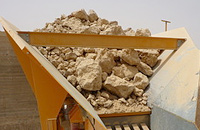
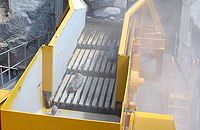
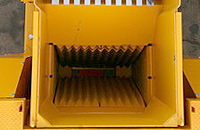

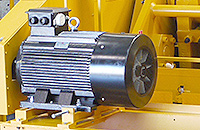
Mobile Jaw Crushers
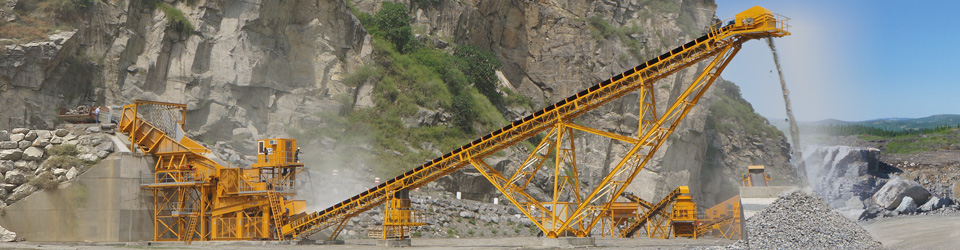
RockRanger RQ & RE
The wheeled RockRanger is a high-capacity, extremely mobile crushing unit suitable for demolition, quarry or gravel feed application.
Mounted on a robust, semi-trailer chassis, a Parker RockSizer or RockSledger primary jaw is combined with a matched, high strength feeder/grizzly and integral product conveyor to give owners portable primary crushing at its best.
A fully mobile primary crushing plant complete with a Parker Rocksizer or RockSledger single toggle Jaw crusher, built around a strong straight beam chassis with standard supports for feed section, crusher, power unit and conveyor frame. The chassis is complete with access/maintenance platforms to the crusher and power unit and a main operator platform overlooks all stages of operation.
- RE model Conforms to European design standards for road use
- High capacity 'Rocksizer' or 'RockSledger' Jaw crusher
- Improved high performance manganese jaws
- Heavy duty feeder with grizzly section
- Diesel hydraulic drive, all electric or electro-hydraulic
- Wide discharge conveyor/excellent under crusher clearance
- Rapid to relocate, easy to set-up & operate
- Suitable for quarrying, demolition & recycling applications
- With a range of drive options and six jaw sizes to choose from
RockRanger RQ
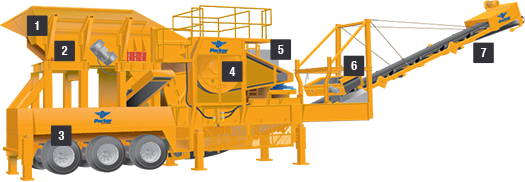
RockRanger RQ
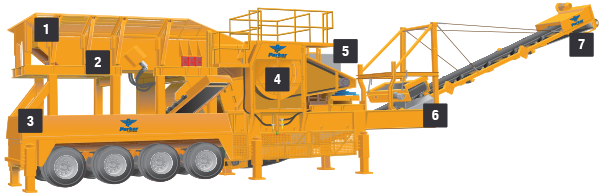
-
1 - Feed Hopper
Externally reinforced heavy duty steel plate hopper. (RE1180 folds down for travelling).
-
2 - Feeder Grizzly
Vibrating feeder with integral grizzly section supported on heavy duty coil springs. The linear movement is imparted to all parts by twin contra-rotating motors.
-
3 - Chassis and Running Gear
Robust fabricated chassis with all necessary operator platforms and access ladders. (the running gear for the RE1180 is quad-axle bogie and the RE1165 is a standard tri-axle bogie). Operating jacks are as standard for levelling the machine.
-
4 - Jaw Crusher
RockSizer (single toggle up-thrust) or RockSledger (single toggle down-thrust) design. Heavy duty reinforced fabricated welded steel plate body. High grade steel eccentric shaft. Hydraulically adjusted jaw settings.
-
5 - Power Unit
Either Electric or diesel hydraulic Caterpillar engine or similar, complete with hydraulic power take off.
-
6 - Over-band Magnet
Powered hydraulically an optional overband magnet is available for clearing metal fragments from crushed material.
-
7 - Product Conveyor
Wide belt conveyor with heavy duty impact idlers under crusher discharge. Lagged head drive pulley with sealed for life bearings on all idlers and bearings. Folds back for travelling.
Crusher Size
|
Maximum Feed Size(mm)
|
Feed Height(mm)
|
Vibrating Grizzly Feeder(mm)
|
Product Conveyor width(mm)
|
Product Conveyor Discharge Height(mm)
|
Power to Drive (kW)
|
Total Machine Weight (tonnes)
|
Weight on the Kingpin/Rear axle (tonnes)
|
Travelling Length (mm)
|
Travelling Width (mm)
|
Travelling Height (mm)
|
RE 800 x 500 |
455 | 4000 | 900 x 300 |
800 | 3320 | 90 | 28 | 11/17 | 9620 | 2500 | *4000 /4550 |
RE 1100 x 650 |
625 | 4000 | 1200 x 4500 |
1000 | 3800 | 110 | 47 | 17/30 | 11590 | 2500 | *4000 /4680 |
RQ 1100 x 760 |
710 | 4500 | 1200 x 4500 |
1000 | 3800 | 110 | 57 | 18/39 | 12220 | 2840 | 4500 |
RE 1100 x 800 |
760 | 4540 | 1200 x 5000 |
1000 | 3800 | 110 | 58 | 18/40 | 13020 | 2500 | *4000 /4540 |
RQ 1100 x 800 |
760 | 4500 | 1200 x 4500 |
1000 | 3800 | 110 | 57 | 18/39 | 12220 | 2840 | 4500 |