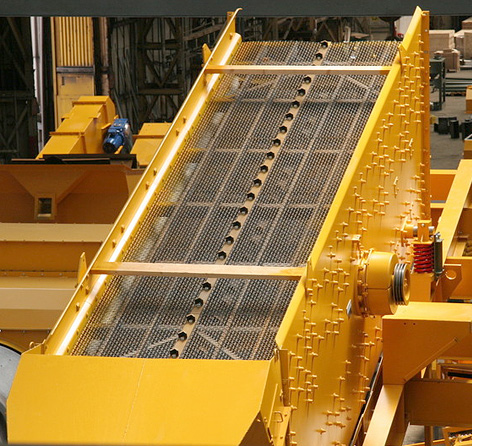
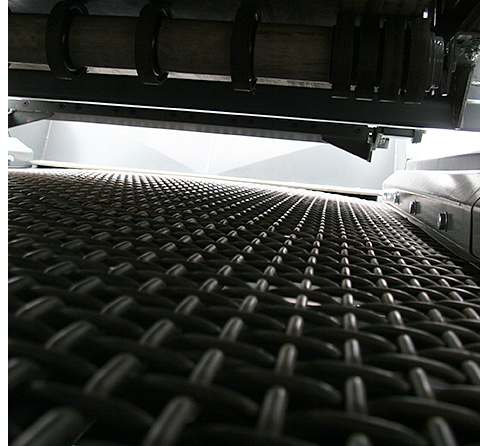
Inclined Vibrating Screens
Highly efficient and extensively field proven with six screen sizes allowing screening efficiency to be matched closely to production requirements.
Parker have been designing and manufacturing vibrating aggregate grading screens for over 50 years and its Rapide range of machines is at the forefront of the need to provide an efficient screen with features ensure good results and effectiveness in the application required.
The final product screening in any aggregate plant is at the heart of the process and an efficient, trouble free machine will provide maximum production of required materials.
Base Screen Units
Rapide Screens
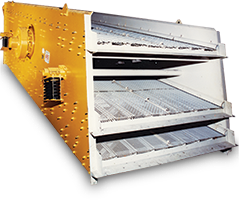
The Rapide range has developed from Parker’s vast experience in this field of equipment and includes many key features to benefit the user:
- Robust screen box construction with all major components assembled using reliable “Huck” fastener system.
- Welded cross members and deck frames are stress relieved and machined to ensure accurate assembly.
- Self-aligning spherical roller bearings developed specifically for vibrating screen applications are used with positive grease lubrication and labyrinth protection.
- Single, fully machined eccentric shaft assembly with external eccentric weights to allow variation and adjustment of vibration for maximum efficiency and flexibility of application.
- Mesh support bars are adjustable to allow variations in materials and tensioning requirements of optional types of screen deck media.
- Screen supported on high quality coil compression springs to ensure isolation of vibration with mountings allowing adjustability of screen operating angle.
- Feed and discharge trays are fitted as standard to assist with chute distribution of materials.
- Screens include the ability to fit water sprays as standard when application requires.
- Options for mounting within static and mobile plant configurations.
Whilst the Parker Rapide is the workhorse of the company’s screen range and is adaptable to most applications there are specialist uses for screens that are catered for within bespoke ranges that incorporate many of the standard features but add additional specific items for instance:
- Rapide screens for asphalt plants with multi-deck facility and high temperature capabilities.
- Longspread models to allow a distribution of multiple products over storage bins and bays etc.
- Single and two deck, Grizzly heavy duty screens for scalping of larger aggregates in primary crushing installations.
Static / Modular & Mobile Chassis
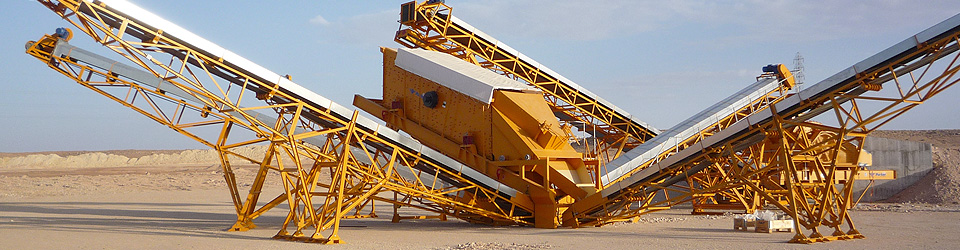
ScreenRanger SA & SF
Featuring the highly efficient and extensively field proven Parker Rapide inclined vibrating screen and available as transportable units for quick on-site positioning and installation.
Parker ‘ScreenRangers’ are a series of static / stationary and mobile screening units featuring the ‘Rapide’ in a number of different sizes. These can have 1, 2 ,3 or 4 decks with discharge chutes tailored to individual preferences, including product blending when required. Every ‘ScreenRanger’ is an independent unit. It can separate up to four sizes plus oversize, according to model.
With six screen sizes to choose from, screening efficiency can be matched closer to production requirements.
Optionally, multi-deck screens can be fitted with discharge blending chutes offering even greater product flexibility by directing graded material and oversize to differing discharge points to facilitate proportional blending of the final graded products.
For wet screening duties, water spray bars can be fitted with the fines collecting chute under the screen being replaced with a fluming chute.
The electric control panel containing the starters for the screen and associated conveyors is mounted on the screen chassis for transport, but when operating, is removed to ground level for vibration-free performance.
- Rugged practical design incorporating the well proven Rapide screen
- Big on output, efficiency & reliability - low on capital outlay and operating cost
- Stress relieved, robust screen box construction
- Withdrawable, easily accessible discharge chute manifold
- Facility for proportional blending of products available
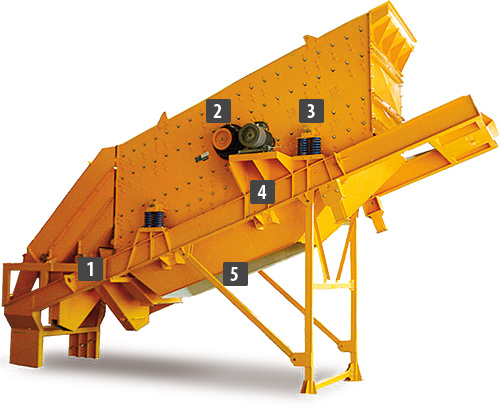
(Static SF model shown)
-
Control Console
The free standing, electrical control console containing starter gear for the screen, and associated equipment is bolted to the plant during transport.
-
Braking System & Front Dolly (Mobile SA Option)
All mobiles are equipped with pneumatic tyred running gear to highway specification, with dual line air brakes and a hand parking brake on the rear wheels. Standard machine semi-trailer; Optional full trailer.
-
Installation
Four rugged lifting brackets are welded to the main chassis to assist during transit and erection
-
Eccentric Shaft
The single activating shaft is eccentric and runs the width of the screen inside a protective steel tube. This tube also acts a substantial structural brace, being set in machined positions in the side plates to ensure the vibration is transmitted positively to the main frame. With eccentric weights the vibrator unit produces optimum amplitude for the majority of duties. Simple addition/subtraction of bolt-on adjustment weights to both sides of the shaft will increase/decrease amplitude for specific requirements.
-
Spring Clamps
The Rapide is a free floating screen, effectively isolated by its springs from the support structure. For transit, the screen is restrained in its angled travelling position by reusable clamp plates (travel brackets) simply bolted across the spring units.
-
Platforms
Optional, open mesh platforms on one or both sides of the machine provide easy access to the screen for maintenance purposes. Complete with galvanized safety hand railing and access ladder.
-
Chute
Several different plant mounted chute arrangements are offered for directing graded material and oversize to separate discharge points. These can include the facility for proportional blending of products, for wet screening duties, the fine chute under the screen is replaced by a fluming chute.
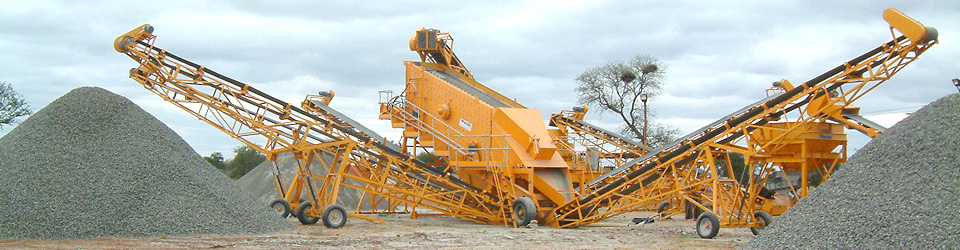
Features
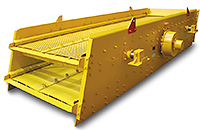
Rapide Design
Every feature of the Rapide is designed to ensure long, efficient service with minimum maintenance with its characteristic parallelogram shape giving more screening area compared to other multi-deck models. Feed and discharge trays are fitted as standard.
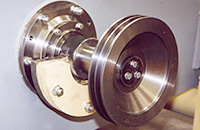
Adjustable Vibration
The eccentric weights on the vibrator units produce optimum amplitude for the majority of duties but the simple addition or subtraction of bolt-on weights on both sides of the shaft will increase/ decrease amplitude for specific requirements.
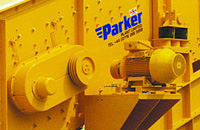
Screen Drive
Drive is totally enclosed, weatherproof electric motor, rated in accordance with data charts, and vee rope transmission. Optional starter is equipped with electric plug braking.
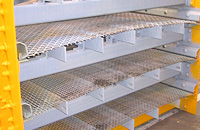
Adjustable Mesh
Adjustable mesh support bars allow fine tuning of mesh camber for varying mesh types.
Specifications
Screen Size (Width x Length) |
Number of Decks | ||||
1 Deck | 2 Decks | 3 Decks | 4 Decks | ||
mm | Inches | ||||
900 x 2000 | 35” x 79” | • | • | • | • |
1200 x 2000 | 47” x 79” | • | • | • | • |
1200 x 3000 | 47” x 118” | • | • | • | • |
1200 x 4000 | 47” x 157” | • | • | • | • |
1500 x 3000 | 59” x 118” | • | • | • | • |
1500 x 4000 | 59” x 157” | • | • | • | • |
1500 x 5000 | 59” x 197” | • | • | • | • |
1500 x 6000 | 59” x 236” | • | • | • | • |
1800 x 4000 | 71” x 157” | • | • | • | • |
1800 x 5000 | 71” x 197” | • | • | • | • |
1800 x 6000 | 71” x 236” | • | • | • | • |
2100 x 5000 | 82” x 197” | • | • | • | |
2100 x 6000 | 82” x 236” | • | • | • | |
2100 x 7000 | 82” x 276” | • | • | • | |
2400 x 5000 | 94” x 197” | • | • | • | |
2400 x 6000 | 94” x 236” | • | • | • | |
2400 x 7000 | 94” x 276” | • | • | • |