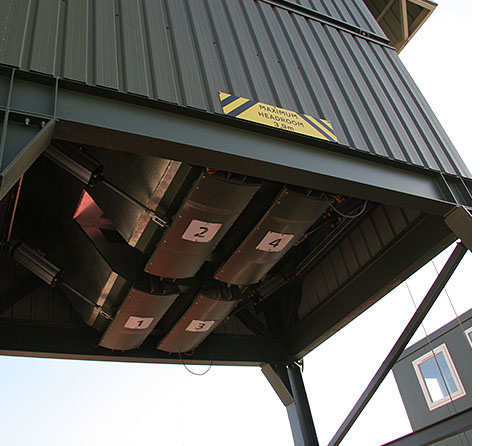
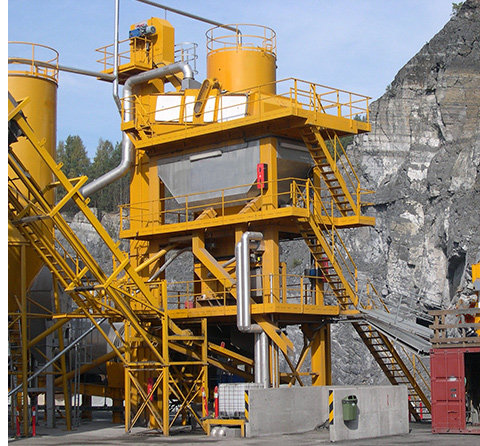
StarBatch
Modular Asphalt Plants
Highly efficient, competitively priced, modular asphalt batch mixing plants.
Ranging in output from 80 TPH to 200 TPH, StarBatch is easy to transport, erect and dismantle.
- Compact low profile modular design
- Fast on-site installation
- External access stairways
- Electronic load cell weighing
- Bitumen injection system
- Efficient, reverse air bag filter with emission levels less than 20mg/m3
- High reliability - low maintenance design
- Can be sheeted to contain dust and reduce noise levels in sensitive locations
The modular concept of the StarBatch range is designed to offer contractors a plant that is easy to transport, easy to erect and easy to dismantle, having the ability to reliably produce quality asphalt for use in more remote locations on either short or long term contracts while at the same time maintaining many of the benefits of a traditional tower plant.
The range includes the StarBatch 1000, 1500, 2000 & 2500. Four models with capacities from 80 to 200 tph, each designed to utilise the full air-flow capacity of the dryer and matching bag filters thereby enabling maximum production capabilities even with elevated moisture in the feed source.
Available with fully sheeted, modular sections, the StarBatch sheeted versions feature integral single or twin filler silos. The hot stone elevator and access stairway are enclosed within the sheeting, improving plant aesthetics and ensuring minimum visual impact on the surrounding environment.
Features
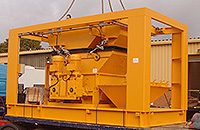
Low Profile Modular Design
Each modular section is pre-wired and factory tested prior to despatch.
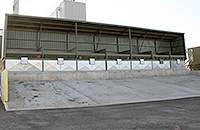
Compact Cold Feed Unit
Compact transportable, multi-compartment, cold feed unit with built in collecting conveyor and dryer feed conveyor. Direct drive geared motor units give high reliability. Accurate variable speed control via AC motor and inverter.
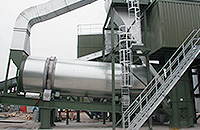
Transportable Aggregate Dryer
Transportable unit with high efficiency internal lifter design, optional insulated and clad drum. Available with a range of advanced design multi-fuel burners.
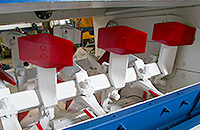
High Efficiency Mixer
Twin shaft, direct geared motor driven, high efficiency paddle mixer. Hard wearing abrasion resistant liner plates, paddle arms and tips. Discharge to truck or mixed material storage facility.
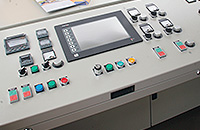
Fully Automatic Control Systems
Range of control options from key pad to PC based, fully automatic systems, with programmable recipe storage.
Options
- Thermal insulation on the aggregate dryer drum
- Environmental sheeting options
- High level option to incorporate mixed material storage
- Heavy oil, gas or multi fuel burners
- RAP and fibre additive systems
Specifications
Units | SB1000 | SB1500 | SB2000 | SB2500 | |
Plant Capacity | |||||
Output1 | tph | 80 | 120 | 160 | 200 |
Cold Feed | |||||
Hopper Capacity (heaped) | m³ | 9.5 | 9.5 | 9.5 | 11.5 |
Hopper Loading Width | m | 3.0 | 3.0 | 3.0 | 3.5 |
Belt Feeder Length | m | 1.5 | 1.5 | 1.5 | 1.8 |
Belt Width | mm | 500 | 500 | 500 | 600 |
Belt Feeder Drive | kW | 2.2 | 2.2 | 2.2 | 3.0 |
Vibrator Fitted to Sand Hopper | YES | YES | YES | YES | |
Collecting Conveyor Width | mm | 500 | 500 | 600 | 750 |
Collecting Conveyor Drive | kW | 4.0 | 5.5 | 5.5 | 5.5 |
Aggregate Dryer | |||||
Dryer Drum Diameter | m | 1.5 | 1.8 | 2.2 | 2.5 |
Dryer Drum Length | m | 6.5 | 7.0 | 8.0 | 9.0 |
Dryer Drive | kW | 22.0 | 30.0 | 4 x 15.0 | 4 x 22.0 |
Dryer Capacity | tph | 90 | 130 | 180 | 220 |
Air Volume | |||||
Dryer | m³/h | 29,080 | 41,885 | 62,600 | 67,365 |
Mixing Section | m³/h | 7,650 | 9,550 | 9,990 | 12,623 |
Total | m³/h | 36,730 | 51,435 | 72,590 | 79,990 |
Hot Stone Elevator, Screen & Mixing Section | |||||
Elevator Capacity | tph | 90 | 130 | 180 | 220 |
Elevator Drive | kW | 11.0 | 11.0 | 15.0 | 22.0 |
Screen Decks | No. | 2 / 31/2* | 2 / 31/2* | 2 / 31/2* | 2 / 31/2* |
Screen Length | m | 3.0 / 4.0* | 4.0 | 5.0 | 6.0 |
Screen Width | m | 1.5 / 1.5* | 1.8 | 1.8 | 1.8 |
Screen Drive | kW | 7.5 / 11.0* | 11.0 / 15.0* | 11.0 / 15.0* | 15.0 / 18.5* |
Hot Storage Capacity | t | 20 | 35 | 40 | 45 |
Hot Storage Bins | No. | 4 / 6 | 4 / 6 | 4 / 6 | 4 / 6 |
Aggregate Weigh Hopper Capacity | kg | 1250 | 1750 | 2250 | 2750 |
Bitumen Weigh Hopper Capacity | kg | 150 | 290 | 350 | 500 |
Filler Weigh Hopper Capacity | kg | 200 | 320 | 450 | 650 |
Paddle Mixer Capacity | kg | 1250 | 1750 | 2250 | 2750 |
Paddle Mixer Drive | kW | 2 x 11.0 | 2 x 18.5 | 2 x 22 | 2 x 37.0 |
¹ Plant capacity is based on 3% moisture content of feed aggregate with 0.5% residual moisture content of mixed materials, dryer discharge temperature of 160°C, ambient temperature 15°C at altitude 150m above sea level, aggregate bulk density average 1600kg/ m³, 5% bitumen content, 45 second weigh/mix cycle at 100% plant utilisation.
* Optional 3½ deck screen