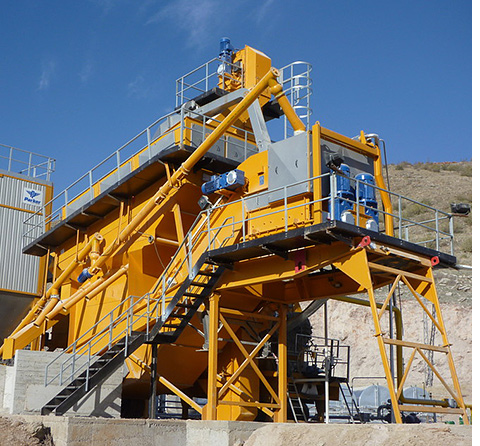
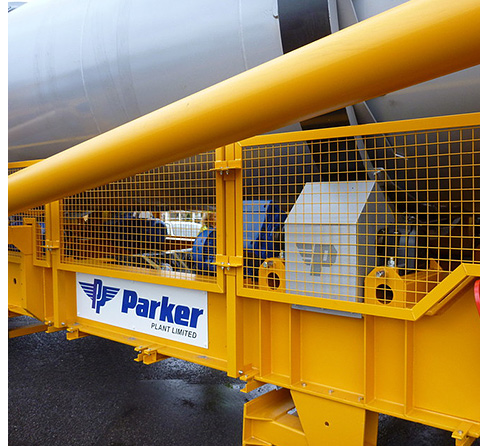
RoadStar 1500/2000/3000
Mobile Asphalt Plants
Mobility, efficiency, reliability and speed. Producing the highest quality asphalt in a wide range of mixes.
3 chassis configuration portable/mobile wheeled asphalt batch mixing plants with outputs from 80 to 240 TPH.
The RoadStar combines quality and mobility to provide one of the most reliable and easily transported asphalt mixing plants available anywhere in the world.
Designed to satisfy the needs of contractors who demand nothing less than the best quality asphalt which is within specification at all times, the RoadStar is the ideal solution for major road and motorway construction projects. Requiring minimal foundations the RoadStar has been a particular favourite for many international airport surfacing contracts across the world.
The three main units of the plant - cold feed, dryer and mixing sections - are fully mobile and on arrival at site can be brought quickly into operation. Their field proven design offers high reliability with low maintenance.
Features
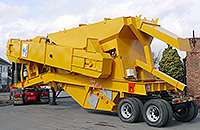
Easily Transportable
Designed with total mobility in mind, each chassis can be easily transported from site-to-site and rapidly put back into operation.
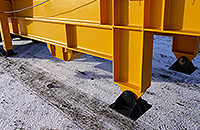
Chassis Landing Legs
Minimum foundations are required for installation as each unit has landing legs with support bases to ensure adequate stability.
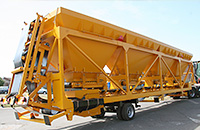
Multi Hopper Mobile Cold Feed
Multi-hopper, road mobile cold feed unit with built in collecting conveyor and dryer feed conveyor. Direct drive geared motor units give high reliability. Accurate variable speed control via AC motor and inverter.
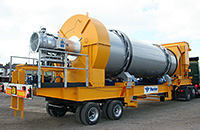
High Efficiency Aggregate Dryer
Road mobile unit with high efficiency internal lifter design, optional insulated and clad drum. Integrated primary dust cyclones and highly efficient burner all on one chassis.
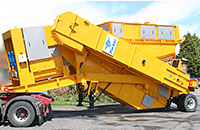
Low Level Mobile Mixing Section
Low-level, mobile unit with integral vertical hot elevator, which folds down for travelling. Heavy duty screen with fully sealed dust housing. Batch weigh hoppers for aggregate, bitumen and filler; all load-cell mounted. Fully synchronised twin shaft direct geared paddle mixer.
Options
- Thermal insulation on the aggregate dryer drum
- Heavy oil, gas or multi-fuel burners
- Mobile or transportable secondary dust filtration systems
- Mobile/static bitumen, filler or mixed material storage systems
- Hydraulic jacking legs to raise the mixing section
Specifications
Units | RS1500 | RS2000 | RS3000 | |
Plant Capacity | ||||
Output* | tph | 120 | 160 | 240 |
Cold Feed | ||||
Hopper Capacity (heaped) | m³ | 10.0 | 10.0 | 12.0 |
Hopper Loading Width | m | 3.0 | 3.0 | 3.5 |
Belt Feeder Length | m | 1.7 | 1.7 | 1.7 |
Belt Width | mm | 500 | 500 | 650 |
Belt Feeder Drive | kW | 2.2 | 2.2 | 3.0 |
Vibrator Fitted to Sand Hopper | YES | YES | YES | |
Collecting Conveyor Width | mm | 500 | 650 | 650 |
Collecting Conveyor Drive | kW | 5.5 | 5.5 | 7.5 |
Aggregate Dryer | ||||
Dryer Drum Diameter | m | 1.8 | 2.2 | 2.5 |
Dryer Drum Length | m | 7.0 | 8.0 | 9.0 |
Dryer Drive | kW | 30.0 | 4 x 15.0 | 4 x 22.0 |
Dryer Capacity | tph | 140 | 180 | 260 |
Air Volume | ||||
Dryer | m³/h | 41,885 | 62600 | 80,760 |
Mixing Section Including Filler Silo | m³/h | 9,550 | 9,990 | 12,600 |
Total | m³/h | 51,435 | 72,590 | 93,360 |
Hot Stone Elevator, Screen & Mixing Section | ||||
Elevator Capacity | tph | 130 | 170 | 240 |
Elevator Drive | kW | 7.5 | 11.0 | 15.0 |
Screen Decks | No. | 2 (4 size + rejects) | 2 (4 size + rejects) | 2 (4 size + rejects) |
Screen Length | m | 4.0 | 5.0 | 6.0 |
Screen Width | m | 1.5 | 1.8 | 2.1 |
Screen Drive | kW | 7.5 | 11.0 | 18.5 |
Hot Storage Capacity | t | 12 | 17.7 | 28 |
Hot Storage Bins | No. | 4 | 4 | 4 |
Batch Elevator Capacity | tph | 130 | 170 | 240 |
Batch Elevator Drive | kW | 7.5 | 7.5 | 15.0 |
Aggregate Weigh Hopper Capacity | kg | 1500 | 2000 | 3000 |
Bitumen Weigh Hopper Capacity | kg | 290 | 300 | 480 |
Filler Weigh Hopper Capacity | kg | 320 | 350 | 630 |
Paddle Mixer Capacity | kg | 1500 | 2000 | 3000 |
Paddle Mixer Drive | kW | 2 x 18.5 | 2 x 22.0 | 2 x 37.0 |