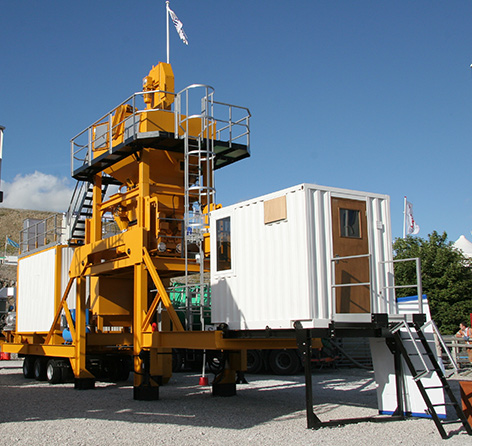
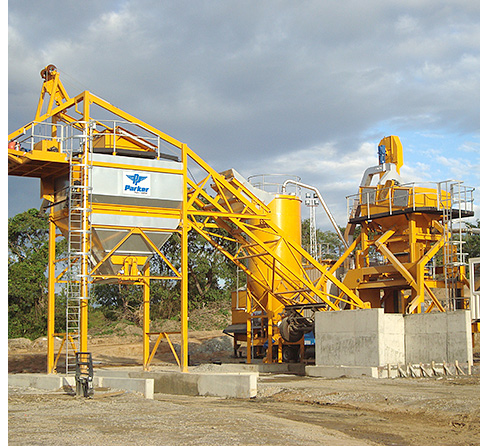
RoadStar 1000
Mobile Asphalt Plants
With a 4 hour installation time, the wheeled, twin chassis RoadStar 1000 can have you at full production within a day of arrival on site.
Portable/mobile asphalt batch mixing plants with outputs of up to 80 TPH
Four independent feed hoppers, dryer and automatic burner are mounted on one chassis while the other carries the vertical elevator, screening, weighing and mixing tower, control cabin, primary cyclones and secondary bag filter.
Installation and erection of the main components is achievable in four hours and with the addition of a bitumen tank and reclaimed filler silo the plant can be put into full production within a day of arrival on site
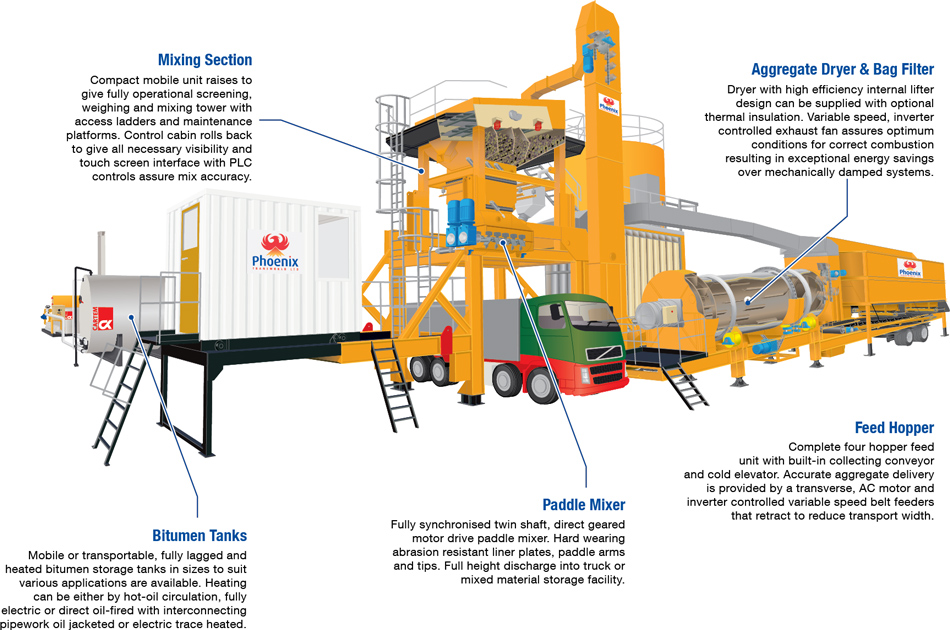
Features
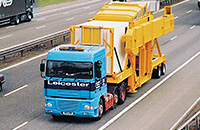
Easily Transportable
Designed with total mobility in mind, each chassis can be easily transported from site-to-site and rapidly put back into operation.
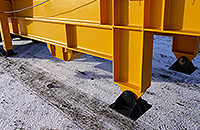
Minimal Foundations
Minimal foundations are required for installation as each unit has landing legs with support bases to ensure adequate stability.
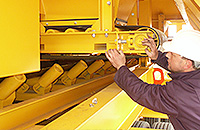
Unique Cold Feed
Set-up involves raising the spillage plates and rolling out the belt feeders. Once secured they can feed onto the collecting conveyor.
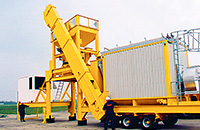
Pivoting Hot Stone Elevator
The entire mixing section is raised into position by crane and the hot stone elevator rotated into the vertical position. Optional hydraulics are available to raise the mixing tower.
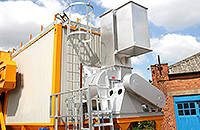
Integrated Dust Filtration
Primary and secondary dust control is included on the mixing section chassis of the 2 chassis M1000 model. Parker bag filters are guaranteed to achieve less than 20mg/Nm³.
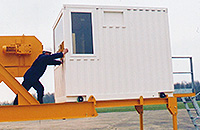
Roll-Out Control Cabin
The control cabin of the M1000 is rolled out to provide better visibility. Hand railing is assembled to provide access.
Options
- Thermal insulation on the aggregate dryer drum
- Heavy oil, gas or multi-fuel burners
- Mobile or static bitumen filler systems
- Mobile or static mixed material storage systems
- Hydraulic jacking legs to raise the mixing section
Specifications
Plant Capacity | |||
Output* | tph | 80 | |
Cold Feed | |||
Hopper Capacity (heaped) | m³ | 5.0 | |
Hopper Loading Width | m | 3.0 | |
Belt Feeder Centers | mm | 1200 | |
Belt Width | mm | 500 | |
Belt Feeder Drive | kW | 2.2 | |
Vibrator Fitted to Sand Hopper | YES | ||
Collecting Conveyor Width | mm | 500 | |
Collecting Conveyor Drive | kW | 2.2 | |
Aggregate Dryer | |||
Dryer Drum Diameter | m | 1.5 | |
Dryer Drum Length | m | 6.5 | |
Dryer Drive | kW | 22.0 | |
Dryer Capacity | tph | 80 | |
Air Volume | |||
Dryer | m³/h | 22,400 | |
Mixing Section | m³/h | 6,100 | |
Total | m³/h | 28,500 |
*Plant capacity is based on 3% moisture content of feed aggregate with 0.5% residual moisture content of mixed materials, dryer discharge temperature of 160°C, ambient temperature 15°C at altitude 150m above sea level, aggregate bulk density average 1600kg/m³, 5% bitumen content, 45 second weigh/mix cycle at 100% plant utilisation.
Note: Bag Filter Specification listed separated
Hot Stone Elevator, Screen & Mixing Section | |||
Elevator Capacity | tph | 90 | |
Elevator Drive | kW | 7.5 | |
Screen Decks | No. | 2 (4 size + rejects) | |
Screen Length | m | 3.0 | |
Screen Width | m | 1.5 | |
Screen Drive | kW | 7.5 | |
Hot Storage Capacity | t | 8 | |
Hot Storage Bins | No. | 4 | |
Aggregate Weigh Hopper Capacity | kg | 1000 | |
Bitumen Weigh Hopper Capacity | kg | 200 | |
Filler Weigh Hopper Capacity | kg | 200 | |
Paddle Mixer Capacity | kg | 1000 | |
Paddle Mixer Drive | kW | 2 x 11.0 |